Unveiling the World of Tungsten-Nickel-Copper Alloy
I. Definition and Compositional Analysis of Tungsten-Nickel-Copper Alloy
Tungsten-Nickel-Copper Alloy is an alloy with tungsten as its matrix, to which small amounts of nickel, copper, and other chemical elements are added. It combines multiple excellent properties, playing a key role in numerous industrial fields.
In common W-Ni-Cu alloy formulations, the addition ratio of nickel to copper is typically 3:2. This specific ratio is not arbitrary but is the result of extensive experimentation and practical validation, achieving an optimal balance among various properties. With tungsten as the primary component, its content usually ranges from 85% to 99%. This endows the alloy with the fundamental characteristics of tungsten, such as its high melting point (up to 3410°C) and high density (19.3 g/cm³). The addition of nickel effectively enhances the alloy's strength and toughness while also improving its machinability. The role of copper is also significant; it not only increases the alloy's electrical and thermal conductivity but also helps regulate its density and coefficient of thermal expansion, resulting in a more superior overall performance.
For instance, W-Ni-Cu alloy components used in some high-end electronic devices have stringent requirements for electrical conductivity and thermal stability. By precisely controlling the content ratio of nickel and copper, and adding trace amounts of other elements, the alloy can be tailored to meet these demanding performance needs, ensuring the stable operation of electronic devices in complex working environments.
II. Showcase of Tungsten-Nickel-Copper Alloy Properties
Density: W-Ni-Cu alloy boasts a remarkable density, with a specific gravity typically ranging from 16.5 to 18.75 g/cm³, making it a true high-density alloy. This characteristic is crucial in applications requiring added weight or center-of-gravity stabilization. For example, in the aerospace sector, certain components of satellites and aircraft are made from W-Ni-Cu alloy to serve as balance weights. By adjusting the weight distribution of these parts, the stability and maneuverability of the aircraft are ensured during high-speed flight or complex orbital operations.
Strength: W-Ni-Cu alloy exhibits excellent strength, with a tensile strength reaching 700-1000 MPa. This means it can withstand significant tensile forces without fracturing. In high-pressure, high-load environments, such as key structural parts for deep-sea exploration equipment or drill bits in oil extraction, its high strength ensures stable and reliable operation, effectively extending the service life of the equipment and reducing maintenance costs.
Excellent Thermal Conductivity: The thermal conductivity of W-Ni-Cu alloy is outstanding. This property makes it highly effective in thermal management for electronic devices. For instance, heat sinks for computer CPUs and substrates for high-power LED lights made from W-Ni-Cu alloy can rapidly dissipate heat, ensuring electronic components operate within a suitable temperature range. This improves the stability, reliability, and lifespan of the devices.
Good Electrical Conductivity: W-Ni-Cu alloy possesses good electrical conductivity, leading to its widespread use in the electronics and electrical industries. Applications include electrical contacts in high-voltage switches and electrodes for electrical discharge machining (EDM). The alloy can operate stably under high-current, high-voltage conditions, ensuring the proper functioning of power transmission and electrical equipment.
Low Coefficient of Thermal Expansion: The coefficient of thermal expansion (CTE) is a key metric for a material's dimensional stability under temperature changes. W-Ni-Cu alloy has a low CTE, allowing it to perform exceptionally well in environments with large temperature fluctuations by maintaining high dimensional stability. In components like high-temperature parts of aero-engines or precision components in electronic devices, which experience drastic temperature changes during operation, a high CTE could lead to deformation or damage. W-Ni-Cu alloy's low CTE effectively prevents these issues, ensuring the stable operation of the equipment.
Good Machinability and Weldability: Unlike many other high-performance materials, W-Ni-Cu alloy features good machinability and weldability. This allows it to be shaped into complex parts and structures using conventional machining processes like turning, milling, drilling, and grinding, meeting the diverse needs of various industries and products. Furthermore, its ease of welding allows for reliable joining with other metallic materials, facilitating the manufacture of large, structurally complex products such as large structural components in aerospace or multi-layer circuit boards in electronics, thereby significantly improving production efficiency and product quality.
III. Application Fields of Tungsten-Nickel-Copper Alloy
1. Aerospace Sector
In the cutting-edge aerospace sector, where material performance requirements for components are exceptionally stringent, W-Ni-Cu alloy's outstanding combination of properties—including high melting point, high strength, good thermal stability, and resistance to thermal fatigue—makes it an ideal material for manufacturing critical components.
2. Electronics Sector
With the advancement of electronic technology, the trend towards miniaturization and higher performance has placed greater demands on heat dissipation and stability. W-Ni-Cu alloy is widely used in the electronics sector due to its unique advantages. In devices such as computers, smartphones, and servers, core components like processors and graphics cards generate significant heat during operation. If not dissipated effectively, this heat can compromise the device's performance, stability, and lifespan. The excellent thermal conductivity of W-Ni-Cu alloy allows heat sinks and thermal spreaders made from it to rapidly transfer heat away, which is then dissipated by fins or fans. This effectively lowers the temperature of electronic components, ensuring stable and reliable operation even under prolonged high-load conditions. Additionally, in electronic circuits requiring high precision and stability, such as those in precision measurement instruments and high-end electronic products, this alloy is used to make resistors. Its good conductivity and stable resistance characteristics ensure that the resistor provides a constant resistance value under varying operating conditions, guaranteeing the reliable functioning of the electronic circuit.
3. Power and Electrical Sector
In the power industry, equipment must operate reliably under complex conditions including high voltage, high current, and high temperatures, imposing strict requirements on materials. Thanks to its excellent high-temperature stability and good electrical conductivity, W-Ni-Cu alloy is a prime choice for manufacturing components like high-temperature resistors, resistance sheets, and electrical connectors. In high-voltage transmission lines, high-temperature resistors are often made from W-Ni-Cu alloy. They maintain a stable resistance value in high-temperature environments and can withstand high currents and power, ensuring the normal operation of the power system. An example is the current-limiting or voltage-dividing resistors used in high-voltage substations. As critical components connecting various electrical elements in power equipment, electrical connectors made from this alloy maintain excellent conductivity and contact stability under high current and voltage. This reduces contact resistance and energy loss, helps prevent electrical accidents, and ensures the reliable operation of power equipment.
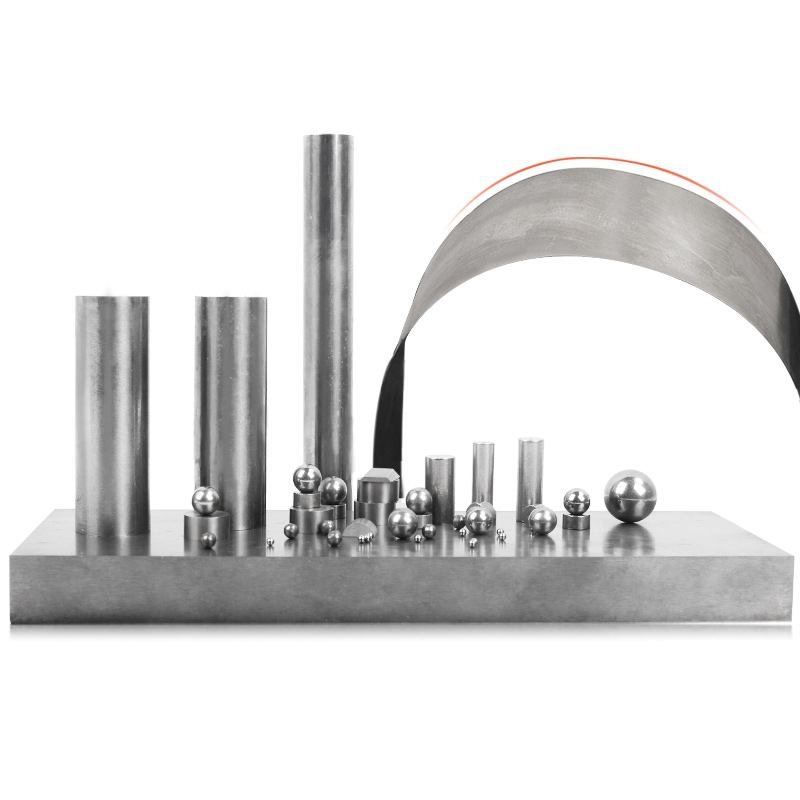
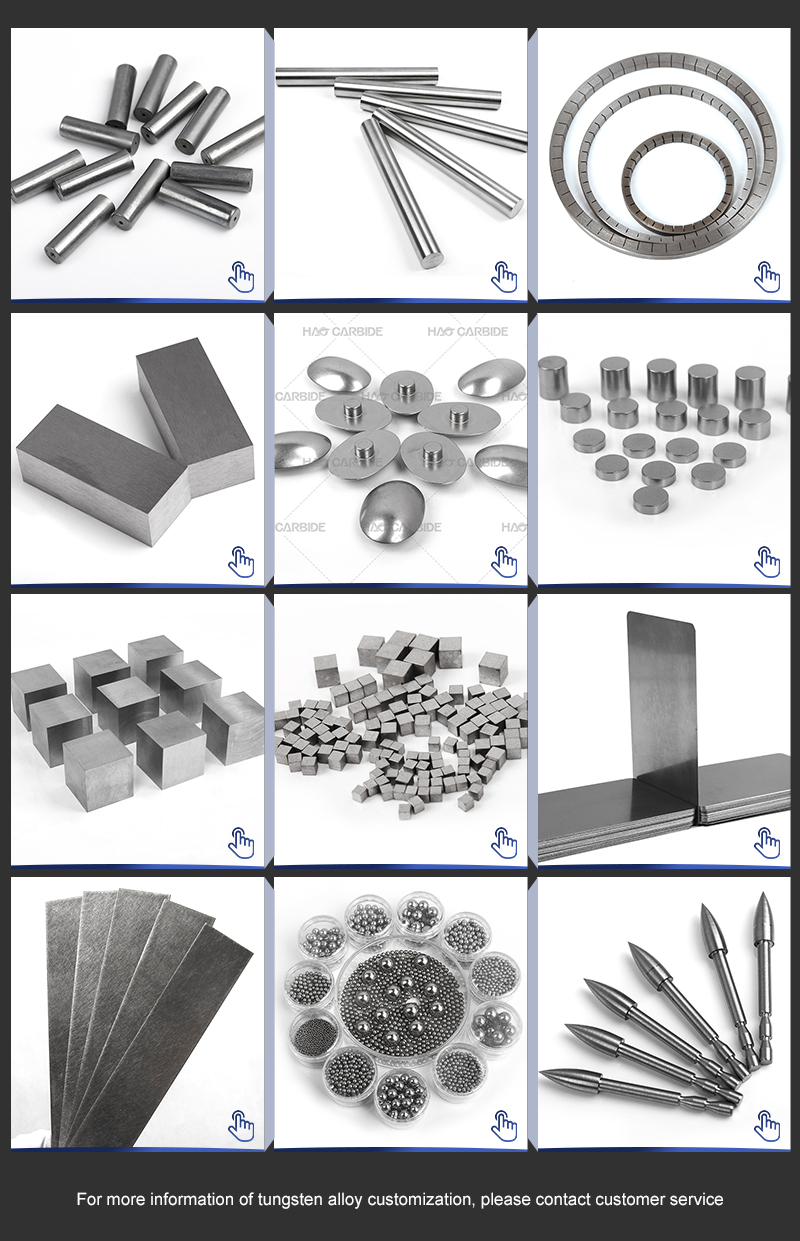
Carbide Rods Products
All Categories
- Ground Solid Tungsten Carbide Rods
- Unground Solid Tungsten Carbide Rods
- Tungsten Carbide Rods Single Hole
- Tungsten Carbide Rods Double Holes
- Nonstandard Tungsten Carbide Rods
- Tungsten Carbide Bars And Strips
- Tungsten Carbide Plates
- Customized Tungsten Carbide Products
- Tungsten Carbide Burr Blank
- Tungsten Weight
- Tungsten carbide rods&Custom-made Carbide rods
- Cemented Carbide Plates & Non-Standard Custom-made Carbide Plates
- Cemented Carbide Strips & Non-Standard Custom-made Carbide Strips
- Cemented Carbide Die & Non-Standard Custom-made Carbide Die
Contact Us
HAO Carbide Co., LTD.
Catherine Tang
Tel: +86-731-22199705
Fax: +86-731-28260602
Mob: +86-13975383023
Email: Catherine@haocarbide.com
Web: www.hao-carbide.com
Address: Building 3, Power Valley Industrial Park, Zhuzhou City, Hunan Province, China